Types of Waste According to Lean Manufacturing and How to Reduce Them?
Alex Niemczyk
—
11/5/2024
Lean is a philosophy of management that has gained worldwide recognition for its effectiveness in optimizing processes and minimizing waste. The core idea of Lean is to focus on delivering value to the customer while simultaneously eliminating actions that do not contribute to that value. A key element of this methodology is identifying and reducing waste (Japanese: Muda), which generates additional costs, prolongs process execution time, and decreases organizational efficiency.
In practice, Lean distinguishes eight types of waste that can occur in any company, regardless of industry. Eliminating them enables companies to operate faster, more efficiently, and with greater employee engagement. In this article, we will discuss each of these types of waste and provide specific ways to reduce them, helping your organization achieve higher quality and improved efficiency.
1. Overproduction
Overproduction, often regarded as the most critical type of waste, occurs when a company produces more products than are currently needed or produces them before they are required. This leads to excess inventory, which incurs additional storage costs and increases the risk of product expiration, damage, or customer disinterest. Lean emphasizes "just-in-time" (JIT) production, meaning items are produced in the necessary quantity and at the exact time they’re required by customers. Streamlining production processes to align with actual market demand is crucial to addressing overproduction and reducing associated costs.
How to Reduce Overproduction?
- Implement Just-in-Time (JIT) Production: Align production closely with actual customer demand, producing only what is needed when it's needed.
- Use Demand Forecasting and Data Analysis: Leverage data to better predict demand, adjusting production rates accordingly to avoid creating excess inventory.
- Apply Kanban Systems: Use Kanban boards or cards to signal when more items need to be produced, thus controlling production flow and preventing overproduction.
2. Excessive Transportation
Transportation waste refers to unnecessary movement of materials, raw goods, components, or products between different stages of production or locations. This can arise from inefficient spatial organization, excessive inventory, or poorly designed facility layouts. While some transportation is inevitable, unnecessary transport adds no value to the final product. Lean seeks to minimize distances and instances of transportation wherever possible by analyzing material flows and optimizing facility layouts to reduce time, energy, and costs associated with unnecessary movement.
How to Mitigate Excessive Transportation?
- Optimize Facility Layout: Arrange workstations and departments to minimize unnecessary travel distances between stages of production.
- Implement Value Stream Mapping (VSM): Map the entire production process to identify and eliminate excess transport steps.
- Utilize Cross-Functional Teams: Bring related functions closer together to reduce the need for materials to be moved long distances.
3. Waiting
Waiting waste is created by production downtime when employees, machines, or materials are idle, waiting for the next step in the process. Causes can include delayed supplies, unavailable resources, equipment failures, or ineffective scheduling. Waiting results in wasted time and potential revenue loss, making its elimination a top priority in Lean. Solutions include standardized workflows, effective scheduling, and real-time monitoring systems that track material flow and resource allocation to minimize idle time.
How to Reduce Waiting Time?
- Standardize Workflow and Processes: Create predictable workflows where each step is clearly defined, reducing delays between tasks.
- Invest in Real-Time Communication Tools: Use software or tools that track and communicate the progress of each stage, helping to identify bottlenecks immediately.
- Use Load Balancing: Distribute tasks across teams and machines to prevent work from piling up in specific areas, reducing downtime.
4. Excess Inventory
Excess inventory is the storage of more materials, semi-finished products, or completed goods than is necessary. This can result from overproduction, inefficient planning, or uncertainty about demand. Excess inventory carries storage costs, ties up capital, and increases the risk of obsolescence or damage. Lean promotes the just-in-time (JIT) approach, which involves supplying materials and producing goods only as they’re needed. While JIT demands a high degree of flexibility and reliable supplier relationships, it can lead to significant reductions in inventory levels and storage costs.
How to Minimize Excess Inventory?
- Adopt Just-in-Time Inventory: Keep inventory levels low by only ordering and stocking materials as they are needed for production.
- Implement a Pull System: Produce items based on actual demand instead of forecasts, controlling inventory at each stage.
- Conduct Regular Inventory Audits: Regularly review inventory levels to adjust for changes in demand or production needs, avoiding accumulation of obsolete stock.
5. Overprocessing
Overprocessing waste occurs when unnecessary steps or more complex processes are performed than required to achieve the desired product quality. An example could be overly detailed polishing of a component when a simpler finish would suffice without affecting the product's function. This waste often stems from a lack of process standardization, use of suboptimal tools, or duplicated actions. Lean encourages examining each production step to ensure simplicity and eliminate all unnecessary operations.
How to Eliminate Overprocessing?
- Standardize Procedures and Training: Ensure that all team members understand the simplest, most efficient ways to complete tasks without adding unnecessary steps.
- Use Root Cause Analysis: Identify why overprocessing occurs, such as unclear specifications or customer requirements, and adjust processes accordingly.
- Apply Value Analysis: Examine each step of the production process to determine if it adds customer value; if not, consider removing or simplifying it.
6. Excess Motion
Excessive motion includes unnecessary movements by employees or machines that do not directly contribute to creating value. Examples include excessive bending, walking, twisting, or repositioning tools. This waste often results from disorganized workspaces, lack of standardization, or poor layout of tools and materials. Implementing the 5S methodology (Sort, Set in Order, Shine, Standardize, Sustain) can help streamline workspaces and reduce excessive motion, improving both worker ergonomics and operational efficiency.
How to Minimize Excess Motion?
- Apply the 5S Methodology: Organize workspaces to ensure everything has a specific place and can be accessed easily, minimizing the need for unnecessary movements.
- Conduct Ergonomic Assessments: Design workspaces and tasks to be ergonomically efficient, reducing the need for excessive stretching, bending, or reaching.
- Standardize Tool Placement: Place frequently used tools and materials within arm’s reach to avoid unnecessary trips or reaching.
7. Defects and Errors
Producing defective items or those requiring rework is one of the most costly types of waste. Defects and errors can stem from malfunctioning machines, poor-quality materials, lack of standardized procedures, or human error. Lean adopts a "zero defects" approach that emphasizes standardization, quality checks at each production stage, and the poka-yoke system (mistake-proofing). The goal is to produce high-quality items on the first attempt, eliminating the need for rework and minimizing financial losses.
How to Prevent Them?
- Implement Poka-Yoke (Error Proofing): Use mistake-proofing techniques, like jigs or sensors, to prevent common errors before they occur.
- Use Root Cause Analysis (RCA): When defects occur, perform a detailed analysis to understand their causes and implement permanent solutions.
- Conduct Regular Quality Checks: Set up quality control checks at every stage of production to catch and correct issues early before they lead to rework or defects.
8. Unused Employee Talent
The eighth form of waste, not officially part of the original Lean framework, is increasingly recognized as "unused talent." This type of waste refers to underutilizing the skills, knowledge, and creativity of employees. Lean emphasizes engaging all team members in process improvement and encourages using their insights to streamline processes. Overlooking employee potential means losing valuable ideas that could lead to innovation and efficiency gains. Involving employees in decision-making and being open to their suggestions can bring substantial benefits to the organization.
How to Utilize Employee Talent?
- Encourage Continuous Improvement: Involve employees in identifying problems and suggesting improvements, which can both tap into their expertise and empower them.
- Provide Training and Development Opportunities: Offer employees the chance to develop new skills or assume more responsibility, maximizing their contributions to the organization.
- Implement Suggestion Systems: Create channels (e.g., suggestion boxes, feedback apps) for employees to share ideas on improving processes, ensuring their insights are heard and valued.
- These strategies enable organizations to systematically identify, reduce, and ultimately eliminate waste across all aspects of their processes. By incorporating these methods, companies can achieve the primary goal of Lean Management: providing maximum value to customers while minimizing unnecessary costs.
How Waste Reduction Impacts Organizations
Reducing waste allows organizations to better utilize resources, shorten production times, and cut costs. The aim is for every stage of the process to add value for the customer. Lean methods help companies achieve a higher level of competitiveness, boost profitability, and increase both employee and customer satisfaction. Notably, Lean isn’t a one-time project but a continuous process of improvement. Adopting Lean requires commitment and consistency, but it yields long-term benefits that can become a critical factor for success in a competitive market.
Conclusion
Eliminating waste is a fundamental principle of Lean methodology. By identifying and eliminating the seven (or eight) types of waste, organizations can significantly enhance their efficiency. Lean’s focus on delivering customer value, minimizing waste, and continuously improving processes makes it a powerful approach to transforming how companies operate. Implementing Lean requires dedication, but the resulting improvements in quality, cost reductions, and flexibility bring considerable advantages, paving the way for a more resilient and competitive organization.
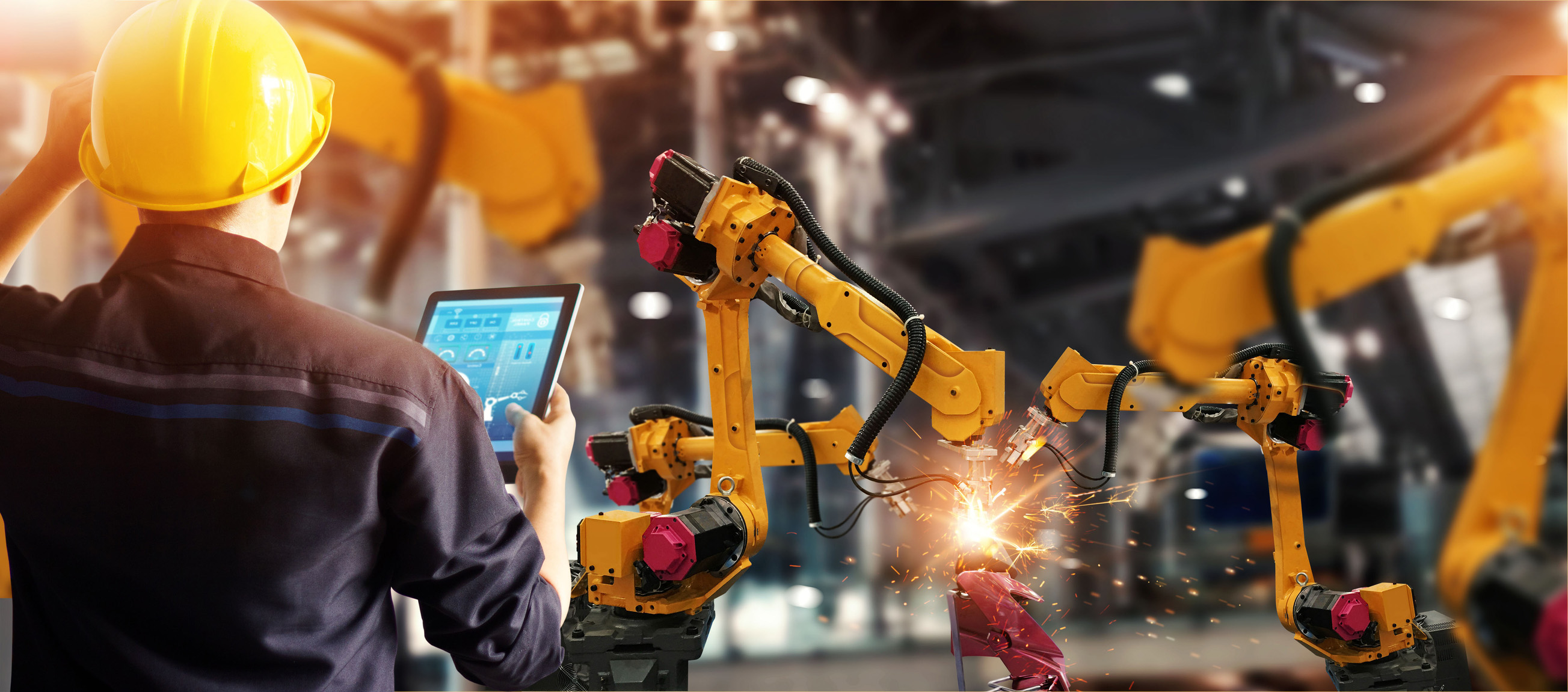
Manufacturing Industry Audit Software
5S, 6S, LPA, and Gemba Walk – proven tools to improve production efficiency, quality, and safety.